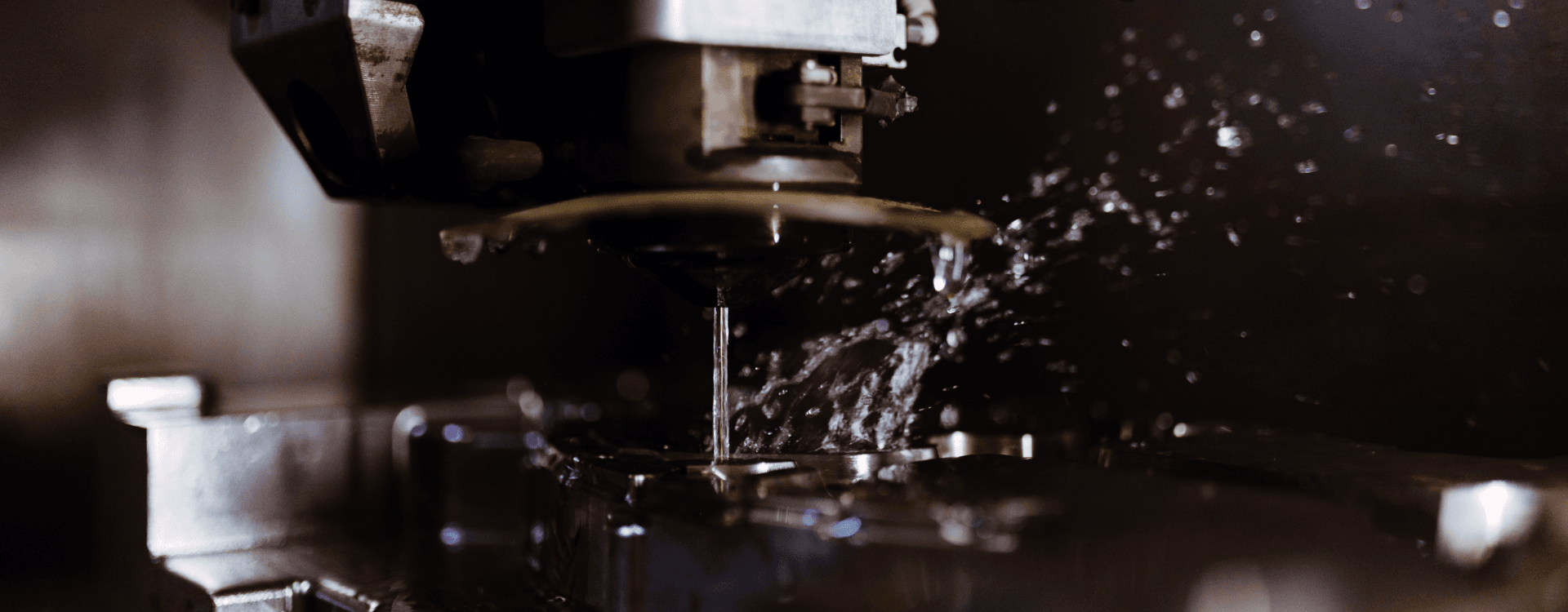
Innovation through
process excellence
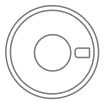
In-house special alloy
We have achieved great success in formulating our high-quality alloy grades specifically to meet the electric vehicle market. These innovative methods helped us attain exceptional elongation properties, an integral part of producing high-quality EV components. As an automotive component manufacturer, our unique alloy composition enables us to produce lightweight, yet robust parts that meet the demands of electric vehicles.
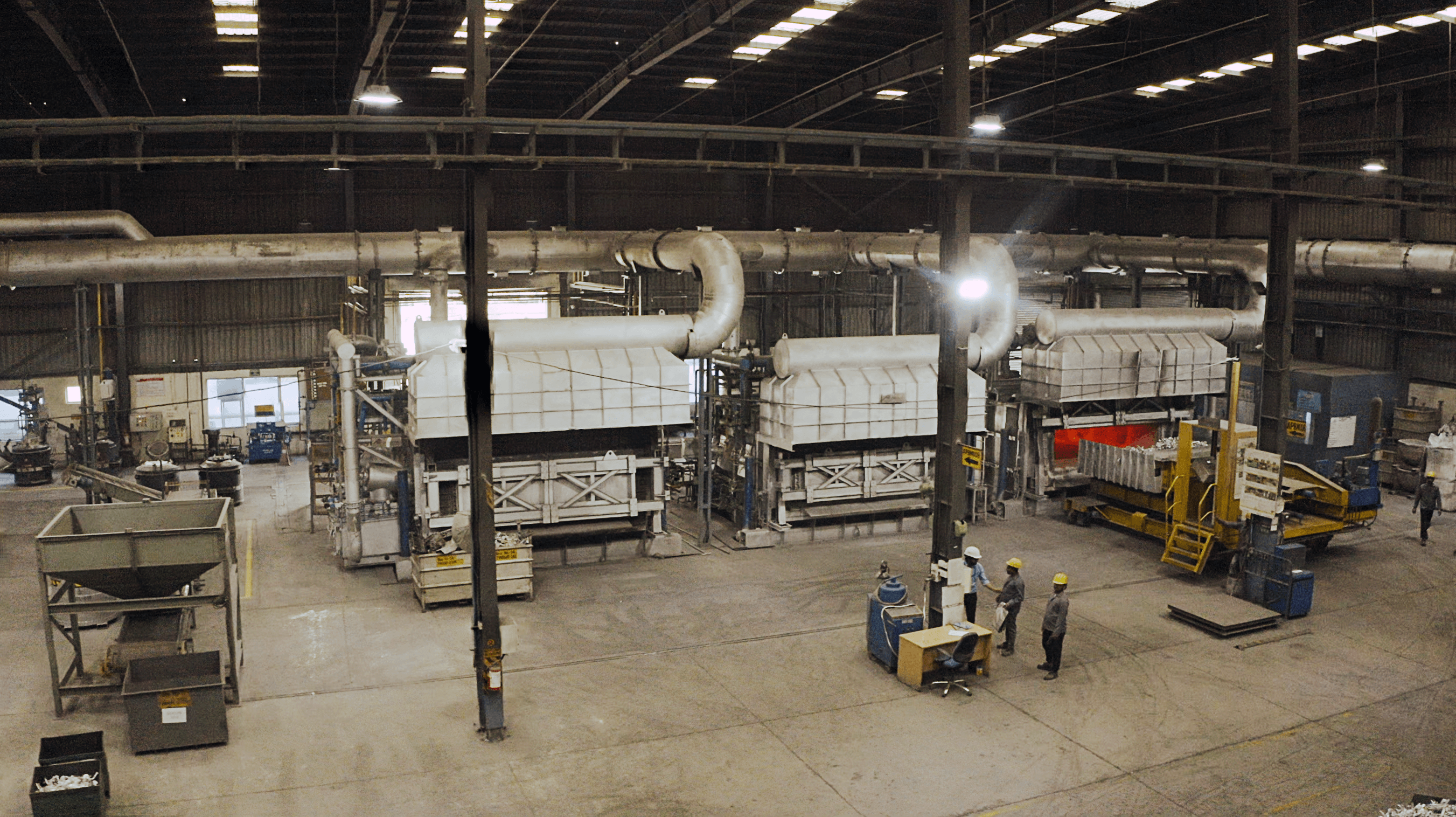
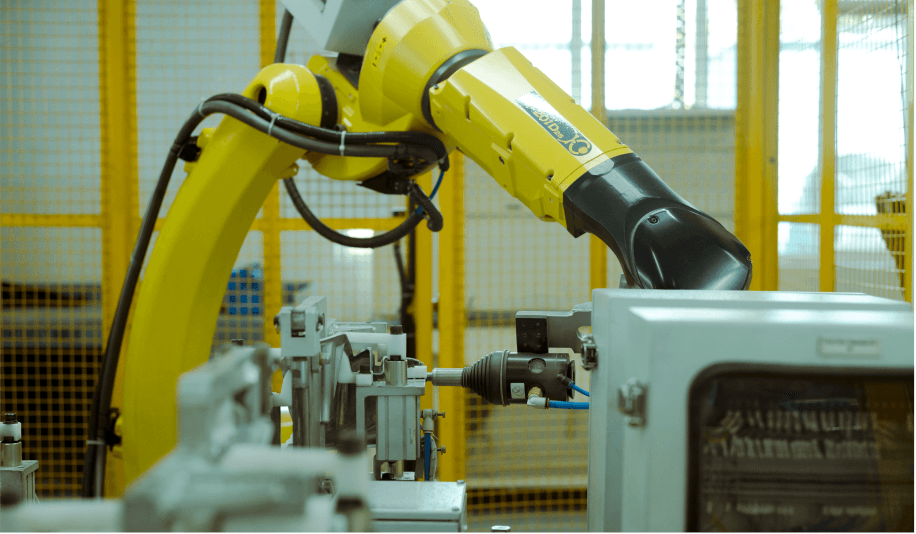
Advancement through technology

Through strategic integration of automation, we have significantly accelerated production, enhanced product quality, and reduced complexities. We understand the rising need for flexible capacity & productivity gains, helping create a more reliable process and improving operational resilience while meeting customer demands efficiently.
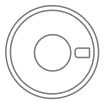
DESIGN SIMULATION
Mold flow simulation allows us to understand aluminium alloy flow & anticipate potential issues that may arise in production and resolve them during the tooling design stage and before mold manufacturing. Die cycling process, mold filling and solidification can be accurately modeled, supporting our role as an automotive component manufacturer.
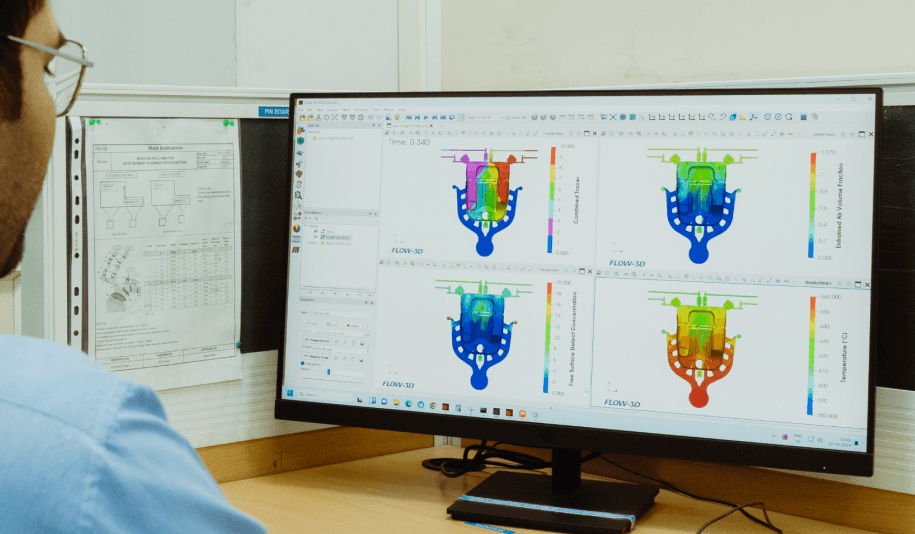
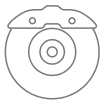
Technology Capabilities
Friction Stir Welding (FSW)
FSW represents a significant leap forward in joining technology. This solid-state process utilizes a rotating tool to generate heat and friction at the joint interface. The targeted heat melts away impurities, forging a robust metallic bond without melting the base materials. This eliminates concerns regarding porosity and cracking associated with traditional welding. Friction stir welding opens doors for applications requiring dissimilar material joining, enhancing Maxop's versatility and commitment to delivering high-quality solutions as a precision auto parts manufacturer.
TECHNOLOGIES IN PIPELINE
RHEO casting
RHEO casting pushes the boundaries of the die-casting industry. This innovative method utilizes a semi-solid metal slurry instead of molten metal. The unique globular structure of the slurry offers significant advantages. It boasts a lower viscosity, enabling intricate part creation with superior mold filling. Furthermore, RHEO casting minimizes porosity, shrinkage, and thermal stress, resulting in exceptional mechanical properties and surface finishes.
Squeeze Casting
This innovative process surpasses traditional methods by aiming for near-zero porosity and exceptional surface finishes. Expected result? High-pressure tightness, exceptional weldability, and the ability to utilize heat-treatable aluminium alloys. To further enhance manufacturing capabilities, we are strategically working in a 1350T vertical squeeze casting machine. This state-of-the-art equipment allows us to produce thick-walled castings suitable for T6 heat treatment.
Counter Pressure Casting
It is an innovative process that combines economy with highly reliable mass production technology to manufacture superior quality aluminum parts. CPC is ideal for products that require a high strength-to-stress ratio to ensure safety and reliability. A perfect application would be chassis parts where high mechanical properties and ductility are needed in a very stable repeatable process. Counter Pressure Casting process uses a combination of pressure and counter pressure to control of mold filling.